Webinar Details $199
- Webinar Length: 100 Minutes
- Guest Speaker: Michael W. Gozzo
- Topic: Purchasing
- Credit: ATAPU 1.50
The role of Purchasing continues to need tools that will make a difference in achieving business improvements. Increasing competitive posture is a necessity to survive.
This program provides a practical tool that will enable an enterprise to achieve significant changes in our relationships with suppliers and our customers.
Your Benefits of Attending:
- Learn how to employ category management in reducing prices.
- Understand why and how to develop trust with suppliers.
- Learn how to address change in a positive and beneficial way.
- Gain insight in the "Targeting Model" for pursuing results.
Join Mike Gozzo as he walks you through the 7 steps to strategic sourcing.
- Introduction
- Content 00:001:42
- Presentation Objective 00:002:32
- Section One - Introduction 00:04:10
- What Is Strategic Sourcing? 00:04:18
- Section Two - Developing Strategies - Step 1 00:05:11
- Four Stages - Supply Management 00:05:28
- Strategic Sourcing Challenges 00:07:46
- Critical Areas 00:11:08
- Creating Time to be Strategic 00:13:02
- Selecting Commodities 00:15:06
- Spend Analysis Framework 00:15:35
- Categorizing Best Opportunities for Strategic Sourcing 00:17:36
- Supply Risk and Profit Impact Model 0019:02
- Section Three - Step - 2 - Developing and Managing Suppliers 00:23:00
- Evaluating Supplier Performance & Capabilities 00:23:38
- Prime Performance Data 00:25:19
- The Role of Supplier Self-Evaluation 00:27:16
- Qualifying the Supplier 00:28:37
- Supplier Checklist 00:29:47
- Checklist Cont’d 00:32:57
- Performance Evaluation 00:35:43
- Evaluation Cont’d 00:38:11
- Section Four - Step 3 - Further Tools 00:41:07
- Lean Supply Chain 00:41:23
- Risk Analysis 00:43:53
- What is an FMEA? Failure Mode & Effects Analysis 00:47:15
- Failure Mode & Effects Analysis (FMEA) 00:48:19
- Understanding “Total Cost” 00:53:25
- Procurement Process Cost Factors 00:54:34
- Commodity Process Cost Factors 00:55:35
- Procurement Operational Performance Costs 00:57:06
- The Impact Of Suppliers On Total Company Costs 01:00:59
- Simplified Income Statement 01:01:56
- Modified Statement 01:02:26
- Supplier Role In Quality 01:03:01
- Impact On Inventory 01:03:46
- Carrying Cost 01:06:23
- Section Five - Step 4 Technology Enablers 01:08:41
- SRM - Supplier Relationship Mgt. Technology 01:09:04
- SRM Technology 01:10:46
- Benefits Of Managing SC Network Relationships 01:13:16
- Benefits of Managing SC Network Relationships Continued 01:14:54
- Section Six - Step 5 Collaborating Internally And Externally 01:15:41
- Collaborative Relationships 01:16:19
- Transforming The Relationship 01:18:33
- Lifetime Customer 01:21:14
- Section Seven - Step 6 Attracting And Retaining Supply Management Talent 01:24:29
- The Future 01:25:07
- Changes In Our Roles 01:26:17
- Skill Sets 01:26:28
- Technology 01:32:07
- Organization 01:32:54
- Section Eight - Step 7 Managing And Enabling The Future Supply Management Organization 01:32:57
- Supply Management Vision 01:36:08
- Supply Management Mission 01:36:44
- Mission Continued 01:38:14
- Supplier/Purchasing Performance Metrics 01:39:07
- Selected Procurement Measures 01:39:57
- Quarterly Business Review (QBR) 01:40:30
- Rules For Success 01:42:38
- Success 01:44:27
- What’s Next 01:46:03
- Recap 01:47:10
- Question & Answer 01:48:45
- Final Comment Reflecting 01:49:07
- Presentation Closing 01:50:50
-
Michael W. Gozzo
Michael W. Gozzo provides consulting and training services to all levels of management and is a Supply Chain Specialist including Purchasing (Supplier Collaboration), Inventory Control and Production/Operations Management. With many years of practical international experience, he offers a supe [...]
ISM Credit
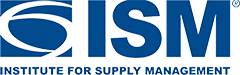
This program may be used for Continuing Education Hours (CEH) toward recertification for programs offered by the Institute for Supply Management®, including the Certified Professional in Supply Management® and Certified Professional in Supplier Diversity®.
ATAPU Credit
Aurora Training Advantage is offering continuing education points designed to recognize dedication to training and excellence in purchasing.QPANJ Credit
Qualified Purchasing Agent - New Jersey
- 80-20 Pareto Rule 00:13:19
- Accounts Payable (AP) 00:55:24
- CIP - Continual Improvement Process 00:30:40, 00:34:39, 01:39:03
- Commodity 00:14:04, 00:15:13, 00:55:41, 01:31:36, 01:41:03
- Cost 00:11:27, 00:26:27, 00:32:51, 00:55:41, 01:01:07, 01:02:50, 00:14:48, 01:25:53
- Electronic Data Interchange (EDI) 00:45:21
- Enterprise Resource Planning (ERP) 00:07:28, 00:15:53, 01:09:26, 01:29:39
- FMEA - Failure Mode and Effects Analysis 00:47:36
- Income Statement 01:01:56
- Inventory 00:17:54, 00:33:36, 00:57:27, 01:01:15, 01:06:40, 01:10:35
- ISO (International Organization for Standardization) 00:24:20, 00:34:45, 01:26:55
- Just In Time (JIT) 00:31:06
- Key Performance Indicator (KPI) 01:39:20
- Lead Time 00:33:27, 00:37:31, 00:57:53
- P-Card 00:16:04
- Procurement 00:16:00, 00:54:37, 01:44:23
- Purchase Order 00:55:08
- Risk Analysis 00:43:55
- Safety Stock 00:57:31
- Spend Analysis 00:15:35
- Strategic Sourcing 00:01:26, 00:04:18, 00:10:04, 00:45:33, 01:49:14
- Supplier 00:04:36, 00:18:55, 00:20:43, 00:23:31, 00:26:12, 00:27:23, 00:35:42, 00:37:23, 00:38:18, 00:41:45, 00:46:32, 00:55:16, 00:59:08, 01:14:12, 01:16:55, 01:41:11
- Supplier Relationship Management (SRM) 01:09:18, 01:10:09, 01:13:38, 01:29:53
- Supply Chain 00:30:23, 00:41:29, 01:15:00, 01:25:04, 01:26:25
- Supply Chain Management 00:05:42
- Total Cost 00:53:34
- Total Quality Management (TQM) 00:31:56, 01:26:58
- Vendor 00:14:30, 01:10:20, 01:16:43
- Vendor Managed Inventory (VMI) 00:45:04, 00:45:49, 01:37:57
- Virtual Management 01:29:34
80-20 Pareto Rule: The Pareto principle states that, for many events, roughly 80% of the effects come from 20% of the causes.
Accounts Payable (AP): The amount of money a company owes creditors (suppliers, etc.) in return for goods and/or services they have delivered.
CIP - Continual Improvement Process: A continual improvement process, also often called a continuous improvement process, is an ongoing effort to improve products, services, or processes. These efforts can seek "incremental" improvement over time or "breakthrough" improvement all at once.
Commodity: A basic good used in commerce that is interchangeable with other goods of the same type.
Cost: The sum of the applicable expenditures and charges directly or indirectly incurred in bringing an article to its existing condition and location
Enterprise Resource Planning (ERP): Refers to a type of software that organizations use to manage day-to-day business activities such as accounting, procurement, project management, risk management and compliance, and supply chain operations.
Failure Mode Effects Analysis (FMEA): Failure mode and effects analysis is the process of reviewing as many components, assemblies, and subsystems as possible to identify potential failure modes in a system and their causes and effects.
ISO (International Organization for Standardization): The International Organization for Standardization (ISO) is an international nongovernmental organization made up of national standards bodies that develops and publishes a wide range of proprietary, industrial, and commercial standards.
Income Statement: One of the three primary financial statements used to assess a company's performance and financial position (the two others being the balance sheet and the cash flow statement). The income statement summarizes the revenues and expenses generated by the company over the entire reporting period. (investinganswers.com)
Inventory: A company's inventory typically involves goods in three stages of production: raw goods, in-progress goods, and finished goods that are ready for sale. Inventory or stock refers to the goods and materials that a business holds for the ultimate goal of resale, production or utilization.
Key Performance Indicator (KPI) : A Key Performance Indicator is a measurable value that demonstrates how effectively a company is achieving key business objectives. Organizations use KPIs at multiple levels to evaluate their success at reaching targets.
Lead Time: The number of days from when a company places an order for supplies, to when those items arrive.
Procurement: Procurement is the process of finding and agreeing to terms, and acquiring goods, services, or works from an external source, often via a tendering or competitive bidding process. Procurement is used to ensure the buyer receives goods, services, or works at the best possible price when aspects such as quality, quantity, time, and location are compared.
Purchase Order: A legal contract between a buyer and a vendor. It lists the materials or services to be purchased on specified terms and conditions (quantity, price / pricing conditions, delivery date).
Risk Analysis: Risk analysis is a technique used to identify and assess factors that may jeopardize the success of a project or achieving a goal.
Safety Stock : Safety stock, also known as buffer stock or backup inventory, is extra inventory that a business keeps in storage to reduce the risk of running out of stock. It can help businesses prepare for unexpected fluctuations in demand, supply chain issues, or inaccurate forecasts.
Spend Analysis: A spend analysis is the process of cataloging business spend data and reviewing it in order to identify inefficiencies, root out unnecessary costs, remove waste and redundancies, and find gaps within the supply chain to make changes that will ultimately reduce costs.
Strategic Sourcing: Strategic sourcing is an approach to supply chain management that formalizes the way information is gathered and used so an organization can use its consolidated purchasing power to find the best possible values in the marketplace and align its purchasing strategy to business goals.
Supplier: A supplier is an entity that supplies goods and services to another organization. A supplier is usually a manufacturer or a distributor. A distributor buys goods from multiple manufacturers and sells them to its customers. Similar Terms. A supplier is also known as a vendor.
Supplier Relationship Management (SRM) : Supplier relationship management is the discipline of strategically planning for, and managing, all interactions with third-party organizations that supply goods and/or services to an organization The objective of SRM is to maximize the value of those interactions.
Supply Chain: A supply chain is a network between a company and its suppliers to produce and distribute a specific product to the final buyer. The supply chain also represents the steps it takes to get the product or service from its original state to the customer.
Supply Chain Management: In commerce, supply chain management, the management of the flow of goods and services, involves the movement and storage of raw materials, of work-in-process inventory, and of finished goods as well as end to end order fulfillment from point of origin to point of consumption.
Total Cost: Total cost is the total expenditure incurred to produce some type of output. From an accounting perspective, the total cost concept is more applicable to financial reporting, where overhead costs must be assigned to certain assets.
Total Quality Management (TQM): Total quality management consists of organization-wide efforts to "install and make permanent climate where employees continuously improve their ability to provide on-demand products and services that customers will find of particular value."
Vendor: A vendor is a person or business that supplies goods or services to a company. Another term for the vendor is the supplier. In many situations, a company presents the vendor with a purchase order stating the goods or services needed, the price, delivery date, and other terms.
Vendor Managed Inventory (VMI): Vendor-managed inventory (VMI) is an inventory management technique in which the supplier of goods, usually the manufacturer, is responsible for optimizing the inventory a distributor holds.
Virtual Management: Virtual management, is the supervision, leadership, and maintenance of virtual teams.
