Webinar Details $199
- Webinar Length: 100 Minutes
- Guest Speaker: Michael W. Gozzo
- Topic: Purchasing
- Credit: ATAPU 1.50
This Supply Chain Management program encompasses the complete spectrum of the functions within this community of diverse activities. A review of the basics necessary to survive are presented. This coupled with understanding what and how to use these tools in concert with the new practices of strategic supply chain that will show the benefits obtained from enterprises successfully employing them.
Emphasis is provided in the management practices of the basic principles of the supply chain coupled with the application of continuous improvement tools.
Your Benefits of Attending:
- Learn what the three (3) key Supply Chain (SC) decision phases are and their respective significance.
- Understand what the major challenges in the SC are and how to successfully overcome them.
- Gain strategies for successfully employing internal operational planning and control tools.
- Learn what is and how to achieve “Lean SC Thinking” by learning from successful deployments.
- Introduction
- Outline 00:01:31
- Objective 00:02:17
- Introduction - Definition & Value of the Supply Chain 00:03:46
- Introduction - Supply Chain Definition and Flow Chart 00:03:51
- Supply and Value Chains 00:06:23
- Power of Supply Chain Management (SCM) 00:15:54
- Basics of SCM 00:12:54
- Principles of Optimal Supply Chains 00:15:32
- Collaboration Implementation - Five Steps 00:21:19
- Collaboration Benefits 00:24:09
- Performance Potential 00:26:52
- Case in Point - Wiremold 00:28:53
- What/How Are You Doing? - Self Assessment 00:32:40
- Self Assessment Cont’d 00:34:31
- Fundamental Concepts 00:34:34
- Strategy 00:34:56
- Four Competitive Attributes 00:35:47
- Considerations 00:37:35
- Order Qualifying Characteristics 00:39:22
- Order Winning 00:40:42
- Operation Environments - Planning Considerations 00:42:06
- Operation Environments 00:42:31
- Customer Order Lead Time 00:43:24
- Operational Layout Definitions 00:47:46
- Constraints Management 00:51:01
- Constraints Management Cont’d 00:52:46
- Three Types of Constraints 00:53:37
- Where is the Bottleneck? 00:57:23
- Inventory - Planning & Control 01:01:34
- Aggregate Inventory Management 01:02:28
- Item Inventory Management 01:04:05
- Inventory Objectives 01:04:50
- ABC Inventory Control 01:06:11
- Principles of ABC Inventory Control 01:07:48
- Inventory Costs 01:08:49
- Item Costs 01:09:09
- Carrying Costs 01:09:49
- Ordering Costs 01:11:51
- Stock-Out Costs 01:14:02
- Logistics 01:15:51
- Logistics Activities 01:16:02
- Role of Warehousing 01:17:05
- Warehousing Process and Activities 01:18:03
- Transportation and Warehousing 01:20:25
- Shipping Patterns 01:21:59
- Shipping Costs 01:22:46
- Logistics & Integration 01:23:24
- Example of Logistics Costs 01:24:54
- Integrated Logistics 01:26:17
- Recap 01:30:10
- Questions and Answers 01:32:05
- Closing Remarks 01:32:39
- Presentation Closing 01:43:42
-
Michael W. Gozzo
Michael W. Gozzo provides consulting and training services to all levels of management and is a Supply Chain Specialist including Purchasing (Supplier Collaboration), Inventory Control and Production/Operations Management. With many years of practical international experience, he offers a supe [...]
ISM Credit
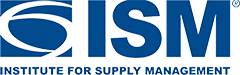
This program may be used for Continuing Education Hours (CEH) toward recertification for programs offered by the Institute for Supply Management®, including the Certified Professional in Supply Management® and Certified Professional in Supplier Diversity®.
ATAPU Credit
Aurora Training Advantage is offering continuing education points designed to recognize dedication to training and excellence in purchasing.QPANJ Credit
Qualified Purchasing Agent - New Jersey
- ABC Inventory Control 01:06:12
- Aggregate Inventory Management 01:02:28
- Constraint 00:51:11
- Constraint Management 00:51:01
- Cost 00:13:57, 00:36:24, 01:08:55
- Inventory 00:24:32, 00:31:33, 00:53:37, 01:02:48, 01:06:37, 01:16:22
- Item Inventory Management 01:04:05
- Lead Time 00:16:46., 00:29:24, 00:43:46
- Pareto Analysis 01:06:18
- Procurement 00:09:13
- Supplier 00:06:41, 00:08:34, 00:16:36, 00:27:13, 00:47:55, 01:12:07
- Supply Chain 00:00:08, 00:01:56, 00:02:25, 00:06:08, 00:09:31, 00:12:19, 00:20:05, 00:32:35, 00:34:35, 01:25:06
- Supply Chain Management 00:01:28
- Value Chain 00:08:48
ABC Inventory Control: ABC analysis is an inventory management technique that determines the value of inventory items based on their importance to the business. ABC ranks items on demand, cost, and risk data, and inventory managers group items into classes based on those criteria.
Aggregate Inventory Management: Aggregate inventory management refers to a basic inventory management method that groups items categories, namely, raw materials, work-in-process, and finished goods. It is also referred to as Aggregate inventory control; it manages multiple individual items under each category.
Constraint: A constraint is anything that limits the degree to which an organization can satisfy its purpose.
Constraint Management: The objective of constraint-based supply planning is to derive an optimal time-phased replenishment plan for all item/locations that achieves desired customer service while respecting inventory policies and real-world constraints at all echelons of the supply chain.
Cost: The sum of the applicable expenditures and charges directly or indirectly incurred in bringing an article to its existing condition and location
Inventory: A company's inventory typically involves goods in three stages of production: raw goods, in-progress goods, and finished goods that are ready for sale. Inventory or stock refers to the goods and materials that a business holds for the ultimate goal of resale, production or utilization.
Item Inventory Management: The process of determining how much of each item you anticipate selling, and when. Once demand is determined, inventory management follows the flow of goods from the supplier through production and ultimately fulfilling customer orders.
Lead Time: The number of days from when a company places an order for supplies, to when those items arrive.
Pareto Analysis: Pareto analysis is a formal technique useful where many possible courses of action are competing for attention. In essence, the problem-solver estimates the benefit delivered by each action, then selects a number of the most effective actions that deliver a total benefit reasonably close to the maximal possible one.
Procurement: Procurement is the process of finding and agreeing to terms, and acquiring goods, services, or works from an external source, often via a tendering or competitive bidding process. Procurement is used to ensure the buyer receives goods, services, or works at the best possible price when aspects such as quality, quantity, time, and location are compared.
Supplier: A supplier is an entity that supplies goods and services to another organization. A supplier is usually a manufacturer or a distributor. A distributor buys goods from multiple manufacturers and sells them to its customers. Similar Terms. A supplier is also known as a vendor.
Supply Chain: A supply chain is a network between a company and its suppliers to produce and distribute a specific product to the final buyer. The supply chain also represents the steps it takes to get the product or service from its original state to the customer.
Supply Chain Management: In commerce, supply chain management, the management of the flow of goods and services, involves the movement and storage of raw materials, of work-in-process inventory, and of finished goods as well as end to end order fulfillment from point of origin to point of consumption.
Value Chain: A value chain is a set of activities that a firm operating in a specific industry performs in order to deliver a valuable product for the market.
