Webinar Details $199
- Webinar Length: 100 Minutes
- Guest Speaker: Michael W. Gozzo
- Topic: Purchasing
- Credit: ATAPU 1.50, QPANJ 2.00, CPE 2.00
How do you know how well your suppliers are doing? Most responses present a subjective view. It is akin to throwing darts—sometimes you are close, but most times you are "off target".
You need a tool that will provide an objective, quantitative visibility of what suppliers are doing. This program will assist purchasing and other areas of business activities in evaluating performance. It will aid you in working with suppliers to improve the quality and availability of products and services.
Take the lead in moving your supply base to a new level of performance. You will be able to quantitatively demonstrate how good—or not so good—your company’s providers of goods and services really are. Discover that by helping your suppliers keep score, all concerned can focus on what is important. This is one more weapon in your arsenal to gain and retain your company’s and your suppliers' competitive edge.
Your Benefits for Attending- Employ Proven Techniques: Learn to monitor key areas of accomplishment effectively.
- Use Rating as a Tool: Discover how to use ratings to establish and improve alliances with suppliers.
- Identify the Best Rating Elements: Understand which rating elements are most effective and why.
- Determine Measurement Frequency: Learn the optimal frequency for measuring supplier performance.
- Select Prime Measurement Criteria: Gain insights on how to choose the most important criteria for evaluation.
- Introduction
- Agenda 00:01:45
- Section 1 00:03:05
- Objective 00:04:00
- Why Improve Supplier Performance? 00:04:30
- Purchasing & Others 00:05:40
- Guidelines for Supplier Improvement Programs 00:06:48
- Goals & Objectives for Supplier Improvement 00:09:23
- Goals and Objectives (Continued) 00:11:08
- Goals and Objectives (Continued) 00:14:26
- Supplier Consideration 00:18:06
- Key Point to Reduce Costs 00:18:24
- Relationships 00:19:31
- Management Involvement 00:21:28
- Key Factors to Consider for Effective Improvement 00:23:18
- Key Factors (Continued) 00:24:59
- Key Factors (Continued) 00:26:51
- Supplier Development 00:28:39
- Collaboration 00:30:59
- Why Do This? 00:31:12
- Results 00:32:04
- Results (Continued) 00:34:17
- Section 2 00:35:42
- Defining the Selection Process 00:35:45
- Measurement & Effectiveness 00:35:59
- Evaluating Supplier Performance & Capabilities 00:36:40
- Developing Criteria for Supplier Selection 00:38:30
- Selection Criteria (Major Categories) 00:38:36
- Prime Performance Data 00:40:21
- Supplier Checklist 00:41:40
- Checklist (Continued) 00:43:44
- Survey the Supplier 00:46:29
- Survey Sample 00:49:15
- Survey Sample (Continued) 00:49:50
- Criteria for Rating System 00:50:26
- Consider 00:51:17
- Consider (Continued) 00:51:46
- Intent of the Criteria 00:53:19
- Intent (Continued) 00:54:11
- Structuring the Importance of Criteria 00:56:59
- Establishing a Scoring Mechanism 00:57:56
- Section 3 00:59:56
- Establishing a Reporting Methodology 00:59:59
- Supplier Rating Report 01:00:25
- Who Uses What & Why? 01:01:26
- Determining Involvement 01:03:23
- Frequency of Reporting 01:04:47
- Three Phases of Improvement 01:05:41
- Phases (Continued) 01:08:48
- Steps to Supplier Development 01:10:44
- Areas Requiring Action 01:10:50
- Creating a Development Board 01:13:35
- Corporate Policy Factors 01:14:15
- Corporate Policy (Continued) 01:16:51
- Procurement Operational Performance Costs 01:17:43
- Reducing the Supply Base 01:23:09
- Why Fewer Suppliers? 01:23:24
- How – Tools to Use for Supplier Reduction 01:24:26
- Timing to Accomplish 01:25:36
- Beginning the Process 01:27:05
- Seven Steps to Supplier Improvement 01:27:32
- Steps (Continued) 01:28:09
- Steps (Continued) 01:29:38
- Supplier Introduction 01:31:05
- Section 4 01:31:48
- Employing the Results 01:31:54
- Utilizing the Information 01:32:10
- Qualifications of a Good Analyst 01:32:45
- Selecting Suppliers - Special Situations 01:33:21
- Reading the Numbers 01:34:46
- Reading the Numbers (Continued) 01:35:59
- Focus Resources for Improvement 01:36:39
- Focus (Continued) 01:37:17
- Developing Competitive Environment 01:38:31
- Competitive (Continued) 01:39:19
- Section 5 01:41:28
- Electronic Linkage 01:41:36
- Implementation Time 01:43:17
- Successful Applications 01:44:03
- Applications (Continued) 01:45:09
- Recap 01:46:24
- Q & A 01:47:48
- Closing Remarks 01:48:18:17
- Thank You 01:49:36
- Presentation Closing 01:49:41
-
Michael W. Gozzo
Michael W. Gozzo provides consulting and training services to all levels of management and is a Supply Chain Specialist including Purchasing (Supplier Collaboration), Inventory Control and Production/Operations Management. With many years of practical international experience, he offers a supe [...]
ATAPU Credit
Aurora Training Advantage is offering continuing education points designed to recognize dedication to training and excellence in purchasing.ISM Credit
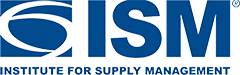
This program may be used for Continuing Education Hours (CEH) toward recertification for programs offered by the Institute for Supply Management®, including the Certified Professional in Supply Management® and Certified Professional in Supplier Diversity®.
QPANJ Credit
Qualified Purchasing Agent - New Jersey
CPE Credit

Aurora Training Advantage is registered with the National Association of State Boards of Accountancy (NASBA) as a sponsor of continuing professional education on the National Registry of CPE Sponsors. State boards of accountancy have final authority on the acceptance of individual courses for CPE credit. Complaints regarding registered sponsors may be submitted to the National Registry of CPE Sponsors through its website: www.nasbaregistry.org.
For more information regarding administrative policies such as complaint and refund, and cancellation please contact our offices at 407-542-4317 or training@auroratrainingadvantage.com.
You must answer all questions during the webinar, view the recording completely and pass the test at the end with 70% correct answers to receive CPE credit.
- 80-20 Pareto Rule 01:24:35
- CIP - Continual Improvement Process 00:42:39
- Commodity 01:13:17
- Cost 00:05:23, 00:13:34, 00:34:11
- Forecast 01:19:14
- Inventory 00:05:10, 00:15:06, 00:17:06, 01:20:10
- Invoice 00:05:16
- ISO (International Organization for Standardization) 00:45:24
- ISO 9000 00:36:40, 01:16:26
- Just In Time (JIT) 00:43:02
- Lead Time 00:14:56, 00:17:04, 01:18:38
- MTBF - Mean Time Between Failures 01:21:57
- Procurement 00:04:42, 01:12:12, 01:17:46, 01:21:45
- Supplier 00:04:58, 00:06:58, 00:12:43, 00:24:59, 00:28:57, 00:35:50, 00:43:41, 00:48:02, 00:56:44, 01:06:55, 01:13:55, 01:23:31, 01:28:54, 01:33:26, 01:43:13
- Supplier Rating System 00:00:08
- Supply Chain 00:05:31, 00:42:11
- Total Cost 00:31:41, 00:52:23, 01:17:14
- Total Quality Management (TQM) 00:13:17, 00:43:33
- Unit Cost 00:52:28
- Value Analysis 00:13:56
80-20 Pareto Rule: The Pareto principle states that, for many events, roughly 80% of the effects come from 20% of the causes.
CIP - Continual Improvement Process: A continual improvement process, also often called a continuous improvement process, is an ongoing effort to improve products, services, or processes. These efforts can seek "incremental" improvement over time or "breakthrough" improvement all at once.
Commodity: A basic good used in commerce that is interchangeable with other goods of the same type.
Cost: The sum of the applicable expenditures and charges directly or indirectly incurred in bringing an article to its existing condition and location
Forecast: A method used to predict inventory levels for a future time period.
ISO (International Organization for Standardization): The International Organization for Standardization (ISO) is an international nongovernmental organization made up of national standards bodies that develops and publishes a wide range of proprietary, industrial, and commercial standards.
ISO 9000: ISO 9000 is a set of standards for quality management systems (QMS) developed by the International Organization for Standardization (ISO). It's a guide for organizations to ensure they meet customer needs and regulatory requirements, and can be applied to any size organization or industry.
Inventory: A company's inventory typically involves goods in three stages of production: raw goods, in-progress goods, and finished goods that are ready for sale. Inventory or stock refers to the goods and materials that a business holds for the ultimate goal of resale, production or utilization.
Invoice: An invoice, bill or tab is a commercial document issued by a seller to a buyer, relating to a sale transaction and indicating the products, quantities, and agreed prices for products or services the seller had provided the buyer. Payment terms are usually stated on the invoice.
Just In Time (JIT): A just-in-time supply chain is one that moves material just before it's needed in the manufacturing process. The technique reduces the need to store excessive levels of materials in a warehouse, and it works best when each operation is closely synchronized with the subsequent operations.
Lead Time: The number of days from when a company places an order for supplies, to when those items arrive.
MTBF - Mean Time Between Failures: MTBF (mean time between failures) is the average time between repairable failures of a technology product. The metric is used to track both the availability and reliability of a product. The higher the time between failure, the more reliable the system.
Procurement: Procurement is the process of finding and agreeing to terms, and acquiring goods, services, or works from an external source, often via a tendering or competitive bidding process. Procurement is used to ensure the buyer receives goods, services, or works at the best possible price when aspects such as quality, quantity, time, and location are compared.
Supplier: A supplier is an entity that supplies goods and services to another organization. A supplier is usually a manufacturer or a distributor. A distributor buys goods from multiple manufacturers and sells them to its customers. Similar Terms. A supplier is also known as a vendor.
Supplier Rating System: A supplier rating system is a formal process that companies use to evaluate and rate the performance of suppliers. The goal of a supplier rating system is to help companies make informed decisions about their supply chain, such as which suppliers to use, how much business to give them, and what prices to pay.
Supply Chain: A supply chain is a network between a company and its suppliers to produce and distribute a specific product to the final buyer. The supply chain also represents the steps it takes to get the product or service from its original state to the customer.
Total Cost: Total cost is the total expenditure incurred to produce some type of output. From an accounting perspective, the total cost concept is more applicable to financial reporting, where overhead costs must be assigned to certain assets.
Total Quality Management (TQM): Total quality management consists of organization-wide efforts to "install and make permanent climate where employees continuously improve their ability to provide on-demand products and services that customers will find of particular value."
Unit Cost : Unit cost encompasses all costs associated with producing or acquiring that item.
Value Analysis: The systematic and critical assessment by an organization of every feature of a product to ensure that its cost is no greater than is necessary to carry out its functions.
