Webinar Details $199
- Webinar Length: 100 Minutes
- Guest Speaker: Michael W. Gozzo
- Topic: Purchasing
- Credit: ISM 1.50, ATAPU 1.50
The pandemic has made visible the weaknesses that have existed for years in the world's supply chain!
We now have a better chance of minimizing the effects of some of the conditions that have persisted and put us on the right track for control. You will walk away with a better understanding of the issues that could be disrupting your supply chain and how to overcome those obstacles.
Your Benefits of Attending:
- Gain a better understanding of the Supply Chain.
- Understand the issues that cause the Supply Chain from operating as it is designed.
- Gain insight into the tools that can help you overcome those issues and how to utilize them.
- Learn the new terminology you will need to understand.
Join Michael Gozzo and start overcoming the obstacles in your supply chain.
- Introduction
- Outline 00:01:37
- Supply Chain Overview 00:03:17
- Supply Chain Flow Chart 00:03:22
- What Are Crisis Experienced? 00:10:56
- Disruption Experienced 00:11:10
- Disruption 00:15:36
- Transportation 00:22:02
- Transportation Action 00:23:57
- Further Practices 00:29:17
- Selecting Commodities 00:31:16
- Supply Risks and Profit Impact Model 00:32:13
- Sourcing Profile 00:34:32
- Spend Analysis Framework 00:35:08
- A-B-C Purchasing Classification Of Value 00:37:26
- Prime Performance Data 00:40:11
- Supplier Checklist 00:41:57
- Supplier Checklist Cont’d 00:43:32
- Strategic Relationships 00:47:14
- Strategic Alliances - Traditional Vs. Strategic 00:50:05
- Strategic Alliances - Considerations 00:51:08
- Strategic Alliances - Complexities 00:53:49
- Strategic Alliances - Proactive Reasons To Form Alliances 00:54:30
- SRM Technology 00:56:45
- Impact Of SRM On Purchasing Roles 00:58:55
- Integrated Supply Chain Networks 01:00:22
- Benefits of Managing SC Network Relationships - Cost Reduction and Demand Enhancement 01:01:34
- Benefits of Managing SC Network Relationships - Agility Improvement 01:04:54
- Benefits of Managing SC Network Relationships - Resolving Conflicts Of Interest 01:06:42
- Roadblocks To Implementing CRM and SRM - Technological Limitations 01:08:56
- Roadblocks To Implementing CRM and SRM - Participant Resistance 01:10:33
- Creating Integrated SC Networks 01:12:48
- Creating Integrated SC Networks - Adopt The Right Attitudes 01:13:59
- Creating Integrated SC Networks - Adhere, Understand, and Focus 01:14:56
- Creating Integrated SC Networks - Business Considerations 01:16:04
- Creating Integrated SC Networks - Cost Considerations 01:17:06
- Creating Integrated SC Networks - Integration Strategy 01:18:49
- Managing Risk In The Supply Relationship 01:21:23
- Collaborative Relationships 01:26:06
- Transforming The Relationship 01:27:26
- Supplier Certification 01:30:09
- Seven Phases Of Supplier Certification - Phases One and Two 01:31:44
- Seven Phases Of Supplier Certification - Phases Three, Four, and Five 01:35:11
- Seven Phases Of Supplier Certification - Phases Six and Seven 01:41:00
- Recap 01:43:20
- Questions and Answers 01:48:55
- Presentation Closing 01:49:08
-
Michael W. Gozzo
Michael W. Gozzo provides consulting and training services to all levels of management and is a Supply Chain Specialist including Purchasing (Supplier Collaboration), Inventory Control and Production/Operations Management. With many years of practical international experience, he offers a supe [...]
ISM Credit
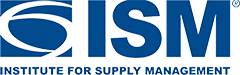
This program may be used for Continuing Education Hours (CEH) toward recertification for programs offered by the Institute for Supply Management®, including the Certified Professional in Supply Management® and Certified Professional in Supplier Diversity®.
ATAPU Credit
Aurora Training Advantage is offering continuing education points designed to recognize dedication to training and excellence in purchasing.- Commodity 00:31:16, 00:34:51
- Critical Infrastructure Protection (CIP) 00:41:57
- Customer Relationship Management (CRM) 01:10:33
- Enterprise Resource Planning (ERP) 00:56:51
- Just In Time (JIT) 00:25:31, 00:43:02
- Management Information System (MIS) 00:50:05
- Master Production Schedule (MPS) 00:03:22
- Materials Requirements Planning (MPR) 00:03:22
- P-Card 00:35:42
- Procurement 00:04:50
- Sales & Operation Planning (S&OP) 00:08:59
- Spend Analysis 00:35:08
- Supplier 00:24:41
- Supply Chain 00:03:23
- Supplier Relationship Management (SRM) 00:08:04, 00:57:02
- Total Quality Management (TQM) 00:41:57
- Transportation Management System (TMS) 00:22:02
- Value Analysis 00:59:34
- Vendor Management Inventory (VMI) 00:08:28
Commodity: A basic good used in commerce that is interchangeable with other goods of the same type.
Critical Infrastructure Protection (CIP): Critical Infrastructure Protection standards compliance framework was developed to mitigate cybersecurity attacks on the Bulk Electric System. While initially, these standards were not required, they were used to mitigate risk, later becoming an industry norm.
Customer Relationship Management (CRM): Customer relationship management is an approach to managing a company's interaction with current and potential customers. It uses data analysis about customers' history with a company to improve business relationships with customers, specifically focusing on customer retention and ultimately driving sales growth.
Enterprise Resource Planning (ERP): Refers to a type of software that organizations use to manage day-to-day business activities such as accounting, procurement, project management, risk management and compliance, and supply chain operations.
Just In Time (JIT): A just-in-time supply chain is one that moves material just before it's needed in the manufacturing process. The technique reduces the need to store excessive levels of materials in a warehouse, and it works best when each operation is closely synchronized with the subsequent operations.
Management Information System (MIS): A Management Information System involves managing the network of interconnected smaller business units, and networks of channels that take part in producing merchandise of a service package required by the end-users or customers.
Master Production Schedule (MPS): Master Production Schedule or MPS is a key planning process in industrial production. It aggregates a large number of variables (customer demand, capacity levels, inventory levels, etc.) and determines what to produce, in what quantity and at what frequency.
Material Requirements Planning (MRP): Material requirements planning (MRP) is a system that helps manufacturers plan, schedule, and manage their inventory during the manufacturing process.
P-Card: A PURCHASING CARD (also abbreviated as PCard or P-Card) is a form of company charge card that allows goods and services to be procured without using a traditional purchasing process. In the UK, purchasing cards are usually referred to as procurement cards
Procurement: Procurement is the process of finding and agreeing to terms, and acquiring goods, services, or works from an external source, often via a tendering or competitive bidding process. Procurement is used to ensure the buyer receives goods, services, or works at the best possible price when aspects such as quality, quantity, time, and location are compared.
Sales & Operation Planning (S&OP): Sales and operations planning is an integrated business management process through which the executive/leadership team continually achieves focus, alignment and synchronization among all functions of the organization.
Spend Analysis: A spend analysis is the process of cataloging business spend data and reviewing it in order to identify inefficiencies, root out unnecessary costs, remove waste and redundancies, and find gaps within the supply chain to make changes that will ultimately reduce costs.
Supplier: A supplier is an entity that supplies goods and services to another organization. A supplier is usually a manufacturer or a distributor. A distributor buys goods from multiple manufacturers and sells them to its customers. Similar Terms. A supplier is also known as a vendor.
Supplier Relationship Management (SRM) : Supplier relationship management is the discipline of strategically planning for, and managing, all interactions with third-party organizations that supply goods and/or services to an organization The objective of SRM is to maximize the value of those interactions.
Supply Chain: A supply chain is a network between a company and its suppliers to produce and distribute a specific product to the final buyer. The supply chain also represents the steps it takes to get the product or service from its original state to the customer.
Total Quality Management (TQM): Total quality management consists of organization-wide efforts to "install and make permanent climate where employees continuously improve their ability to provide on-demand products and services that customers will find of particular value."
Transportation Management System (TMS): A transportation management system (TMS) is a logistics platform that uses technology to help businesses plan, execute, and optimize the physical movement of goods, both incoming and outgoing, and making sure the shipment is compliant, proper documentation is available.
Value Analysis: The systematic and critical assessment by an organization of every feature of a product to ensure that its cost is no greater than is necessary to carry out its functions.
Vendor Management Inventory (VMI): A supply chain agreement where the manufacturer or supplier takes control of the inventory management decisions for the seller or retailer.
